Quality Agreements
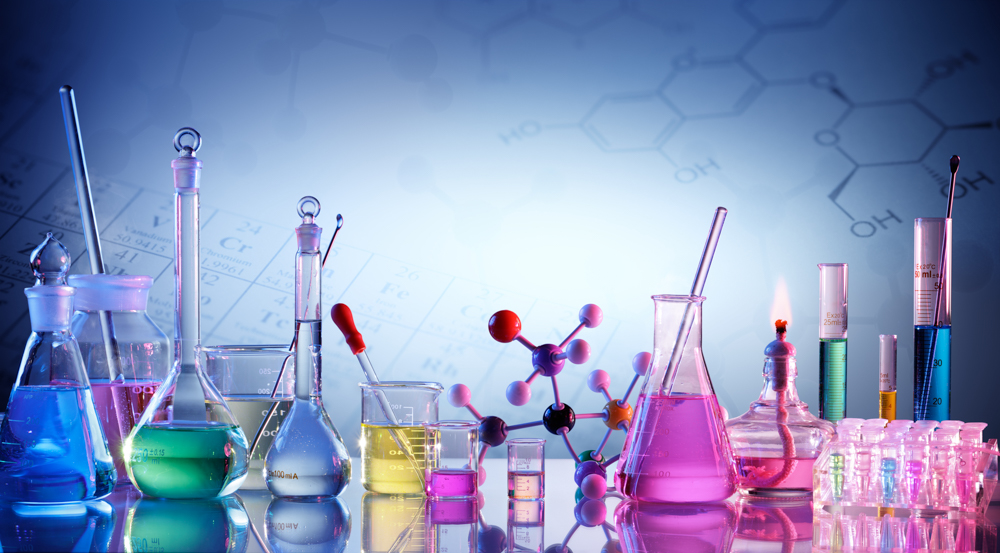
INTRODUCTION
In the present article we summarize what we’ve learned in the period since our earlier article appeared in Journal of GXP Compliance some years ago, entitled “Implementing Quality Agreements at the Contract Laboratory”1. Specifically, here we focus on how the lab gets the Quality Agreement “right” and then follows it throughout its lifecycle by identifying what we call key “check points”. Our experience has shown that there are points in the Quality Agreement process, by which we mean the process of drafting, approving, implementing and revising the Quality Agreement, that are particularly problematic because they require greater attention and/or pose greater risk and it is key to manage these.
Check Point ONE: Prepare to adopt agreements
A major challenge at the contract lab (CRO) is to handle Quality Agreements (QAGs) through some standardized procedure, while at the same time allowing for the diverse needs of a wide client base. This becomes more evident when one considers that the QAG typically originates with the client, in their format, and therefore contains many client-specific idiosyncrasies. Furthermore, the contract lab may be performing laboratory testing under GLP, GMP and/or ISO laboratory testing protocols, which, although greatly similar to one another, will each have its own unique requirements. Procedures, to be useful, must be detailed enough for personnel to be trained on and to follow. However, to be standardized across the wide client base, they must not be too detailed. One cannot have a procedure for each client. Management must therefore “see the forest for the trees”.
Check Point TWO: Check that your quality house is in order
There should already be in place a strong quality program at the CRO and the QAG must make a good fit to this program. Those concerns (terms) that are rather common to Quality Agreements should already be addressed in the existing quality program at the CRO or else consideration must be given to incorporating them into the existing program. This approach is distinctly different and better than leaving them only in the QAG. To leave important concerns only in the QAG is tantamount to instructing the lab to only consider doing such quality work when working on this particular client’s project.
Check Point THREE: Understand the high-risk terms of the specific agreement
Understand and have input into specific terms of the agreement. It is important to make a careful review of the draft. Don’t agree to terms that you cannot meet. Take a team approach in order to foresee any/all difficulties in implementing the terms by involving lab Management, Principal Investigators and Quality Assurance in the draft review. Many of the high-risk terms are those that are specific to the client. By high-risk, we mean at risk of being ignored during the conduct of the study. For example, how and when the client is to be notified of an out-of-specification result is typically client-specific and terms involving notifications to be made to the client are generally high risk. Other terms that are often high risk center around how changes to laboratory procedures, testing protocols and written instructions in general are to be handled and how vendors and other 3rd parties providing materials and/or services in support of the client’s experimental study are to be qualified2.
Check Point FOUR: Train users on Quality Agreements in general and on each specific agreement they will be using
Quality Agreements are to be used. They are not to be put on the shelf and then forgotten. Keep track of who has been trained on each. This can be done with a training matrix. It is a good idea to keep an updated list of the agreements that are active (e.g. the training matrix) in a place highly-visible to all employees. To make it more useful, consider cross-referencing each QAG against the client and perhaps also to the Principal Investigators assigned to the client’s various experimental studies. To protect client-confidentiality, consider using a client code in place of the client name. A mechanism must be in place to ensure that the training is performed on a timely basis. Couple this training to some other required client-based activity that occurs at an appropriate time in the process of taking a client project from start to finish. For example, we start each experimental study using a kick-off meeting facilitated by the Principal Investigator (PI), who is guided by a kick-off meeting checklist3. Listed on the checklist is the requirement to review any applicable QAG. All scientists participating in the study are required to attend and to sign the attendance sheet. The attendance sheet is forwarded to the Training Coordinator, who uses it to update the Training Matrix. Any person missing the training must make it up and this will involve among other things, reading the QAG and passing a quiz on it. Attendance sheets are filed in the employees training binder.
Create an SOP on Quality Agreements. In it, provide background and details on the QAG system in place in general. All employees supporting client studies must be trained on this SOP.
Quality Assurance should keep the original QAG. QAGs are often 20 to 30 pages in length. It is a good idea for the QAU to also keep a one-to-two-page summary of key points appearing in the QAG and to note those points that the QAU anticipates causing more trouble to the lab or that may present a greater risk. The effective start and expiration dates along with client contact information should be included. The summary does not take the place of the QAG.
Check Point FIVE: Identify failures over time and feedback into the CAPA program
Any deviation from a QAG should be considered “major”, requiring a deviation investigation in order to identify root cause and corrective and preventative actions for Management and Quality Assurance review and approval4. The specific QAG will state whether or not the deviation is to be reported to the client and if so, how it is to be addressed with the client. Quality Assurance must query the CAPA database to determine if there is a pattern of failures to follow a specific QAG or QAGs, in general. Such feedback is critical to improving the QAG system and may help to improve specific Quality Agreements. Of course, the more effort put in at the front end to establish a good agreement and to train everyone on it, the less effort needed on the back end. Perhaps more importantly, like any quality system, a good QAG system will scale up with no difficulty as more and more clients desire to put QAGs into place with the lab, whereas a bad system simply will not.
SUMMARY
The effective implementation of a single Quality Agreement and the management of a quality agreement program at the Contract Research Laboratory, requires getting good QAGs into place and monitoring the lab’s performance in implementing them over time. Key to the management process is the identification and understanding of points in the workflow at which to make critical checks.
REFERENCES
- 1. R.C. Wedlich and J. Webb, “Implementing Quality Agreements at the Contract
Laboratory”, Journal of GXP Compliance, Vol. 16, Issue 4, 2012.
- 2. R.C. Wedlich, et al., “Implementing an Effective Provider Qualification Program at the
Contract Laboratory”, Journal of GXP Compliance, Vol. 17, Issue 3, 2013.
- 3. R.C. Wedlich, et al., “Implementing an Effective GLP Program at the Contract Research
Laboratory”, Journal of GXP Compliance, Vol. 19, Issue 2, 2015.
- 4. R.C. Wedlich, et , “Implementing an Effective CAPA Program at the Contract
Laboratory”, Journal of GXP Compliance, Vol. 21, Issue 2, Mar 2017.